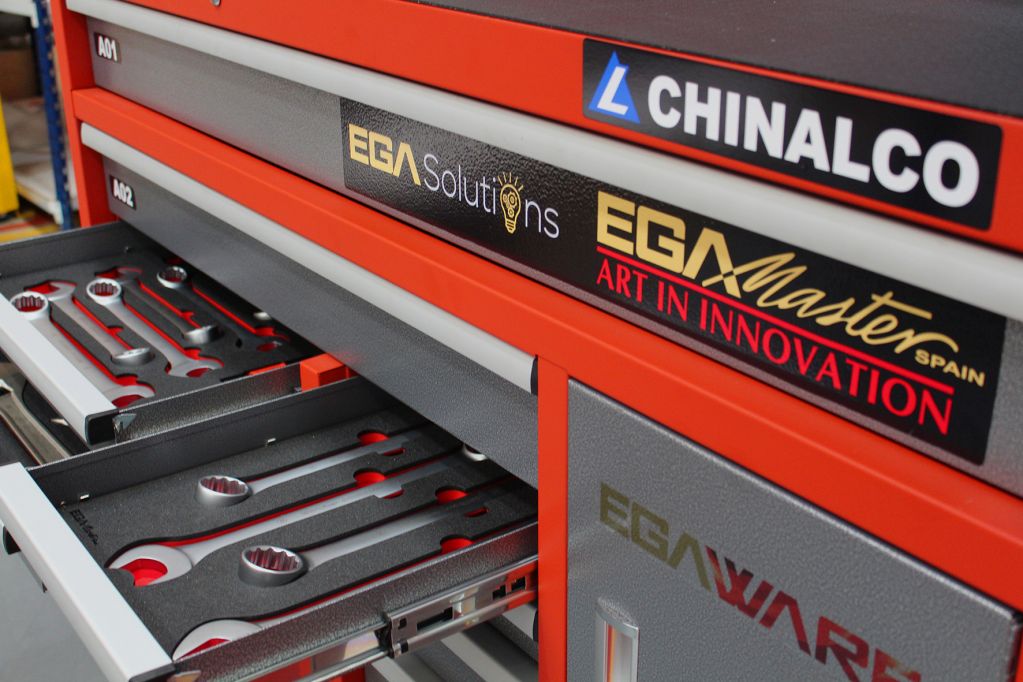
In mining, an unplanned stoppage can result in losses of tens of thousands of euros per hour. But in many operations — especially in regions where safety and maintenance culture is still taking shape — these interruptions don’t always receive the attention they deserve.
Very often, operational stoppages originate from invisible yet constant inefficiencies, such as:
- Tools missing at critical moments
- Tools out of calibration, without traceability
- Poorly located equipment, shared without control or in poor condition
- Improvised, disorganized workshops, with no flow or standards
These situations don’t just affect efficiency. They drastically increase the risk of accidents, especially during maintenance or intervention in critical areas. That’s why advanced tool inventory management is not a luxury or trend: it’s a strategic necessity for operations — and for the safety of workers.
At EGA Master, together with EGA Solutions, we offer an integrated solution based on three pillars:
Custom Bicolor Foam Trays
Custom-designed trays provide instant visual control: every tool has its place. Any absence is detected immediately, reducing losses, improving discipline, and speeding up work. In mining — where every minute counts — visual order is part of the DNA of efficiency.
We've delivered custom projects using these trays to leading companies such as Komatsu in Peru, CODELCO in Chile, Kamoto (Glencore) in the Democratic Republic of Congo, and Newmont in Mexico.
Download the full project gallery developed for the mining industry.
EGAWare: Real-Time Digital Traceability
Our EGAWare software allows full control of location, status, calibration history, and tool usage. It also sends alerts, schedules maintenance, and generates automated reports.
Without data, there is no control. Without control, there is no safety.
We delivered two complete cabinets including the EGAWare Tool Control System for the Truck Shop Maintenance area of CHINALCO Mining — the first EGAWare implementation in South America.
5S Projects: Organized, Standardized Workshops
We apply the 5S philosophy (Sort, Set in Order, Shine, Standardize, Sustain) to transform improvised workshops into high-performance environments. This directly impacts technician motivation, accident prevention, and fault response capacity.
Not implementing these solutions means accepting unnecessary, avoidable risks. From operational delays to incidents that could endanger lives, the cost of disorganization is always higher than the cost of prevention.
In modern mining, smart tool management is not just an improvement — it's a necessary evolution.